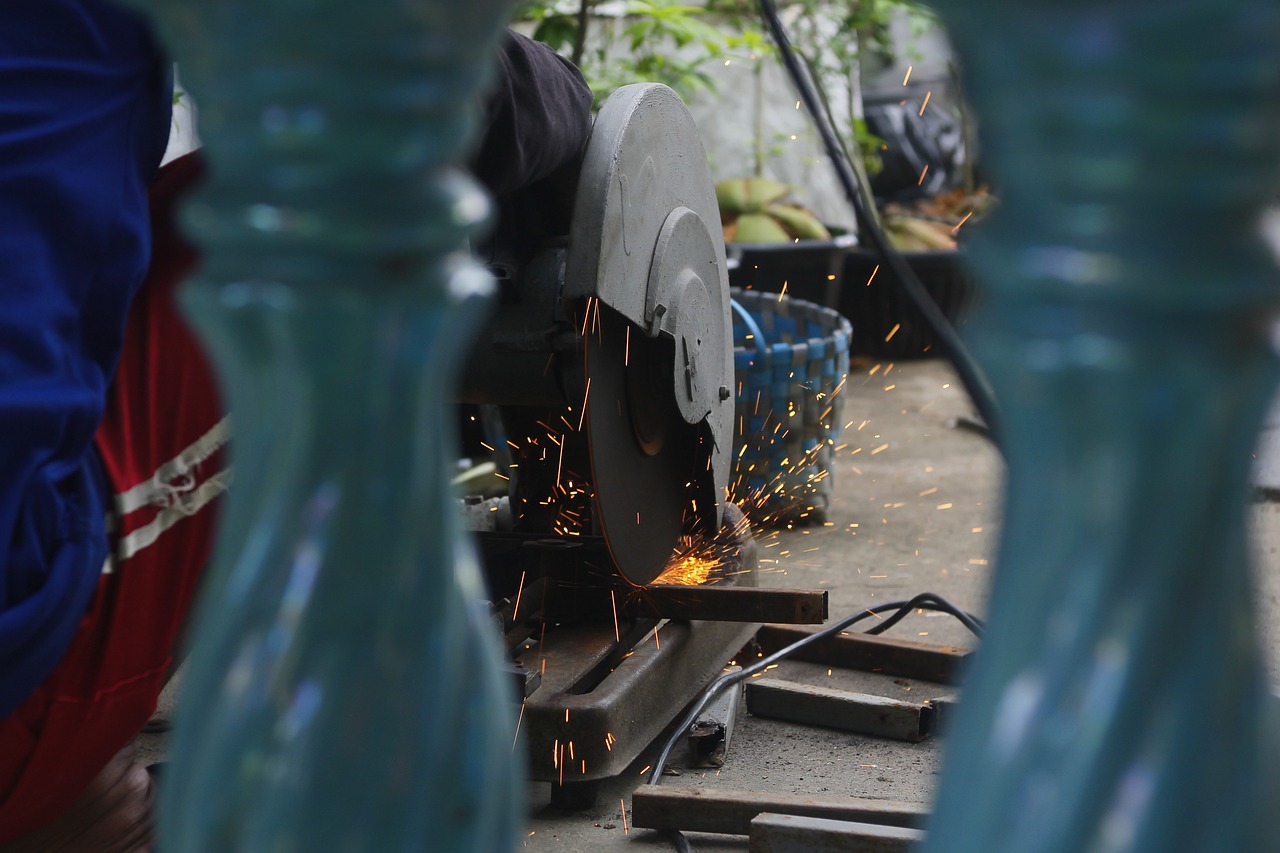
Przecinarki tarczowe są niezwykle popularnymi narzędziami w wielu branżach – od budownictwa po przemysł metalowy.
Ich kluczową zaletą jest możliwość precyzyjnego cięcia różnorodnych materiałów, takich jak metal, drewno, kamień czy beton. Aby jednak przecinarka tarczowa mogła działać efektywnie przez długi czas, niezbędne jest zwrócenie uwagi na jej kluczowe komponenty. W tym artykule omówimy najważniejsze części przecinarek tarczowych, które mają bezpośredni wpływ na ich wydajność oraz trwałość, a tym samym na efektywność wykonywanej pracy.
1. Tarcza tnąca
Najważniejszą częścią przecinarki tarczowej jest oczywiście tarcza tnąca. To ona odpowiada za bezpośrednie cięcie materiału, dlatego jej jakość i odpowiedni dobór mają decydujący wpływ na efektywność pracy. W zależności od rodzaju przecinarki oraz materiału, który ma być przecinany, tarcze tnące różnią się zarówno budową, jak i materiałem, z którego są wykonane.
Na rynku dostępne są tarcze z różnymi powłokami, np. z diamentu, które są dedykowane do cięcia twardych materiałów, takich jak beton czy kamień. Z kolei tarcze ze stali węglowej będą lepsze do pracy z metalami. Kluczowe jest regularne sprawdzanie stanu tarczy – zużycie, odkształcenia lub pęknięcia mogą nie tylko obniżać wydajność cięcia, ale również prowadzić do niebezpiecznych sytuacji.
Odpowiedni wybór tarczy do danego materiału pozwala nie tylko zwiększyć efektywność cięcia, ale także wydłuża żywotność samego narzędzia. Warto także pamiętać, że właściwa konserwacja i okresowa wymiana tarczy są kluczowe dla utrzymania optymalnych parametrów pracy.
2. Silnik
Silnik jest sercem przecinarki tarczowej. To on dostarcza energii niezbędnej do napędzania tarczy i wykonywania cięć. W przecinarkach tarczowych można spotkać zarówno silniki spalinowe, jak i elektryczne. Wybór odpowiedniego silnika ma wpływ na moc urządzenia, co z kolei przekłada się na szybkość i jakość cięcia.
Silniki spalinowe charakteryzują się dużą mocą, co sprawia, że są idealne do ciężkich prac w terenie, takich jak cięcie betonu czy asfaltu. Silniki elektryczne, choć zazwyczaj nieco słabsze, są za to lżejsze i bardziej ekologiczne, co czyni je odpowiednimi do zastosowań w zamkniętych przestrzeniach lub przy pracy z materiałami lżejszymi.
Odpowiednia konserwacja silnika jest kluczowa dla utrzymania długiej żywotności przecinarki. Regularne czyszczenie, wymiana oleju (w przypadku silników spalinowych) oraz kontrola stanu łożysk i wirnika mogą znacząco przedłużyć czas użytkowania narzędzia i poprawić jego wydajność.
3. Przekładnia
Przekładnia, czyli układ, który przenosi moment obrotowy z silnika na tarczę, jest kolejnym istotnym elementem przecinarki tarczowej. Wysokiej jakości przekładnia zapewnia stabilność pracy oraz efektywne przeniesienie mocy z silnika na tarczę. Właściwa konstrukcja przekładni minimalizuje także straty energii, co wpływa na wydajność całego urządzenia.
Nieodpowiednio działająca przekładnia może prowadzić do obniżenia prędkości obrotowej tarczy, a co za tym idzie – gorszej jakości cięcia oraz większego zużycia samej tarczy. Dlatego tak ważne jest regularne smarowanie i konserwacja przekładni, aby utrzymać jej optymalną wydajność. Zaniedbanie tego elementu może prowadzić do kosztownych napraw oraz konieczności wcześniejszej wymiany narzędzia.
4. System chłodzenia
Podczas pracy przecinarki tarczowej, szczególnie w przypadku cięcia twardych materiałów, tarcza i inne elementy urządzenia mogą ulegać znacznemu nagrzewaniu. Z tego powodu większość przecinarek jest wyposażona w system chłodzenia, który odprowadza ciepło i zapobiega przegrzewaniu się narzędzia.
Systemy chłodzenia mogą być wodne lub powietrzne. Wodne systemy chłodzenia są bardziej efektywne i są stosowane głównie w przecinarkach do betonu czy asfaltu, gdzie wymagana jest intensywna praca przy wysokich obciążeniach. Woda nie tylko chłodzi, ale również zapobiega nadmiernemu tworzeniu się pyłu, co zwiększa bezpieczeństwo pracy. Z kolei systemy powietrzne są stosowane głównie w przecinarkach elektrycznych i spalinowych o mniejszej mocy.
Wydajny system chłodzenia pozwala na dłuższą i bezpieczniejszą pracę urządzenia, chroniąc tarczę i inne komponenty przed uszkodzeniami związanymi z wysoką temperaturą.
5. Układ prowadzenia i stabilizacji
Stabilność i precyzja cięcia w przecinarkach tarczowych zależy nie tylko od mocy silnika czy jakości tarczy, ale również od układu prowadzenia. Układ ten umożliwia precyzyjne prowadzenie tarczy wzdłuż linii cięcia, minimalizując ryzyko odchyleń. Ważnym elementem tego układu są prowadnice oraz mechanizmy regulacji kąta cięcia.
Zaawansowane przecinarki tarczowe są wyposażone w systemy laserowego prowadzenia, które pozwalają na jeszcze większą precyzję cięcia, zwłaszcza przy bardziej skomplikowanych pracach. Dobrze skonstruowany układ prowadzenia nie tylko podnosi komfort pracy, ale również wydłuża żywotność narzędzia, ponieważ minimalizuje ryzyko uszkodzenia tarczy przez niekontrolowane ruchy.
6. System zabezpieczeń
Ostatnim, ale równie ważnym elementem przecinarki tarczowej, jest system zabezpieczeń. Nowoczesne urządzenia są wyposażone w szereg mechanizmów, które mają na celu ochronę operatora oraz samego narzędzia. Przykładem mogą być osłony tarczy, które zapobiegają przypadkowemu kontaktowi z wirującą tarczą. Istnieją także systemy automatycznego wyłączania przecinarki w przypadku wykrycia nieprawidłowości, takich jak nadmierne wibracje czy przegrzanie.
Dzięki odpowiednim zabezpieczeniom, praca z przecinarką tarczową jest nie tylko bardziej komfortowa, ale przede wszystkim bezpieczniejsza. Operator ma pewność, że w przypadku awarii urządzenie automatycznie się wyłączy, minimalizując ryzyko uszkodzeń i wypadków – https://przecinarkitarczowe.com.pl/czesci-do-przecinarek-tarczowych-kluczowe-elementy-wydajnosci-i-trwalosci-narzedzi/.
Przecinarki tarczowe to niezwykle wszechstronne narzędzia, które znajdują zastosowanie w wielu branżach. Ich efektywność i trwałość zależą jednak od wielu czynników, w tym przede wszystkim od jakości i stanu kluczowych części. Regularna konserwacja, wybór odpowiednich tarcz, dbałość o silnik, przekładnię oraz system chłodzenia to podstawowe kroki, które mogą znacząco przedłużyć żywotność narzędzia i zwiększyć jego wydajność.